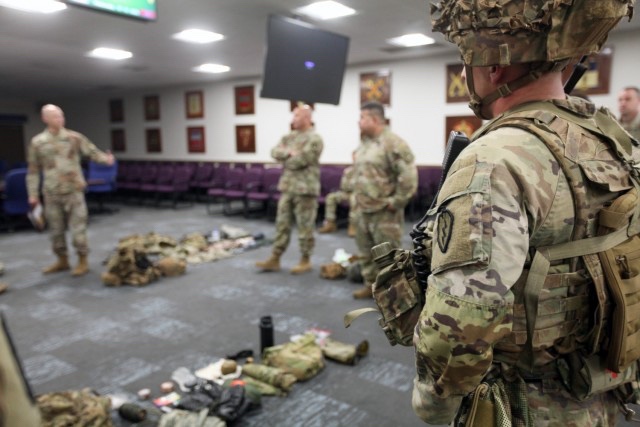
FORT BELVOIR, Va. – The Army is continuing its efforts to modernize the force and build towards the Army of 2030 and beyond. To support that effort, Program Executive Officer (PEO) Soldier is engaging with Soldiers at the ground level to get to the fundamental truth of how Soldiers are equipped in the operational environment and what gear they have modified or purchased for mission, environment, comfort and personal effect.
PEO Soldier’s Assistant Program Executive Officer (APEO) Soldier has been conducting Operational Kit (O.K.) Analysis with the operational force to collect this data.
O.K. Analysis seeks to address a multitude of objectives to help shape the Army of 2030 and the future Soldier. The effort looks to proactively identify opportunities utilizing the Soldier Enhancement Program (SEP), influence materiel change proposals, identify equipment training challenges and address installation Soldier equipment logistics challenges.
“The idea behind O.K. Analysis was hatched by APEO Soldier’s Senior Enlisted Advisor, MSG Josh Kaplan,” said COL Douglas Copeland, Assistant Program Executive Officer, PEO Soldier. “He identified the need to bridge the gap between what we think Soldiers and Squads carry as materiel developers and what is actually used out in the field.”
In launching the initiative, MSG Kaplan took a couple of key steps: First, he created a community of interest across various stakeholders. Second, he worked with SGM Daniel Rose, PEO Soldier Sergeant Major, to combine the O.K. Analysis event with the PEO Soldier Capabilities Demonstration, which informs the force of our current and emerging capabilities in the PEO Soldier portfolio. This strategy allows PEO Soldier to gain Soldier feedback about on operational needs and determine exactly how PEO capabilities are impacting the Force.
The goal is to provide operational context to the acquisition force, said SGM Rose. “We’re trying to explain to the acquisition professionals here at PEO Soldier and stakeholders in the Army enterprise how Soldiers are using the equipment that they are designing, procuring and fielding in the operational environment. What we found is that sometimes they won’t be using the equipment the way it was designed to be used. We try to bring that kind of context back to the acquisition force to help them as they’re designing and procuring new pieces of equipment.”
The O.K. Analysis team kicked off the program at USARCENT in Kuwait in March 2023 and has since engaged with the 11th Airborne and 25th Infantry Divisions. As a result, PEO Soldier has, to date, collected data from eight Squads and worked with senior leadership to establish an equipment baseline across the Army’s operational units.
The effort goes beyond simply questioning Soldiers about their thoughts and experience with PEO Soldier capabilities. MSG Kaplan explained, “We deploy a team of senior NCOs with extensive operational experience and extremely smart government contractors who carry out an array of responsibilities, such as data collection, statistics, logistics and photography. We collect several thousand lines of data, hundreds of photos and several hours of interviews that are analyzed as a part of an out-brief to communities of interest, then added to our holistic database for further analysis.”
After taking part in PEO Soldier’s O.K. Analysis engagement, SGM Brian Disque, G-3, 5 and 7 Sergeant Major, USARCENT, stated that he was very impressed with its effectiveness and potential benefits. He explained, “It is a very ambitious effort to answer an important question: What gear are Soldiers actually using and why? PEO Soldier took the idea of unit outreach and feedback to the next level with a meticulous approach to data collection to better understand the perspectives of Soldiers across the Army. The wealth of data collected will be very useful when informing future efforts to outfit our Soldiers. All of the Army should be grateful that this team was willing to roll up their sleeves and get out to all corners of our Army to answer these questions.”
This effort has already returned positive outcomes. Through the O.K. Analysis initiative, PEO Soldier has been able to strengthen critical partnerships with the Maneuver Center of Excellence, DEVCOM and several Army Corps. PEO Soldier has also been able to facilitate the establishment of Environmental Working Groups with these communities of interest, which include items discovered through the O.K. Analysis effort.
“The most important benefit of O.K. Analysis is to ensure that the Soldier’s voice is heard, including senior leaders in operational units who have important Soldier equipment insights,” Kaplan said. “We do this in the form of detailed equipment inventories, pictures and candid interviews that are shared with the enterprise. If someone asks, ‘Why is Soldier equipment getting heavier?’, our team can say, ‘Let me show you.’ There is a lot of power in that.”
Disque agreed, noting, “For USARCENT and our deployed force, the opportunity to provide our candid feedback to the professional data collection team is of immediate benefit. Innovation is one of our top priorities, and we are always searching for ways to bring innovative concepts to our Area of Responsibility (AOR). Soldier kit is one of those topics for which there is no shortage of great ideas out there, often based on real-world feedback from operating environments across the CENTCOM AOR – you just have to ask the right questions, which I am confident the PEO Soldier team executed to perfection.”
Through this effort, PEO Soldier began an Army-wide innovation synchronization effort that encompasses 18th Airborne Corps’ Eagle Works, I Corps’ Lightning Lab, USARCENT and PEO Soldier’s Soldier Integration Facility. This will allow stakeholders to collaborate and share data and integration solutions across the Close Combat Integration Enterprise (CCIE).
“Any opportunity to connect our modernization efforts to deployed Soldiers on a mission is valuable,” said Disque. “Some of the most innovative ideas come from operating in a deployed environment, and for the PEO team to have access to Soldiers that served recently in Syria and other areas is tremendous.”
Kaplan and his team have proactively submitted proposals for the Soldier Enhancement Program (SEP) on behalf of Soldiers through the O.K. Analysis. The SEP is a process designed to help the Army enhance Soldiers’ ability to execute their combat mission by evaluating prototypes and commercially available items submitted by Soldiers and industry. Since its inception six months ago, PEO Soldier has identified 23 potential SEP opportunities, which is an exponential increase relative to recent years. Soldiers, senior leaders and industry are also able to submit their own proposals utilizing PEO Soldier’s website.
“Soldiers are very innovative,” said Kaplan. “There is always that one Soldier in the Squad who can create ways for his unit to become more lethal. This initiative highlights innovative solutions so communities of interest can stay on pace with the operational force.”
CSM Joseph Gaskin, Command Sergeant Major, 1/11 Airborne Division, added to that assessment by stating, “Any effort the Army uses to better inform equipment requirements from the Soldier on the ground is value added to our formation. The O.K Analysis comprehensive program captured data that will assist leaders to better understand what risk the Soldier’s load presents as we operate in the extreme cold of our operational environment.”
PEO Soldier will continue its O.K. Analysis effort by visiting Soldiers with the 3rd Infantry Division in October and engaging with U.S. Army Europe in the second quarter of 2024. This ongoing effort will collect and share data amongst the CCIE to help shape the Army’s modernization efforts moving into 2030 and beyond.
PEO Soldier is now encouraging other interested U.S. Army operational divisions to reach out and schedule an O.K. Analysis of their area of responsibility.
“We look forward to expanding our O.K. Analysis across the Army’s operational units to further collaboration, leverage creative innovation and enable proactive capability development for Soldier equipment,” said Copeland.
By David Jordan