GRAFENWOEHR, Germany — U.S. Soldiers, Marines, Department of Defense civilians, and troops from the United Kingdom observed and tested a series of unmanned, remote-controlled ground vehicles during a combined training event at Grafenwoehr Training Area, Germany, April 2, 2018.
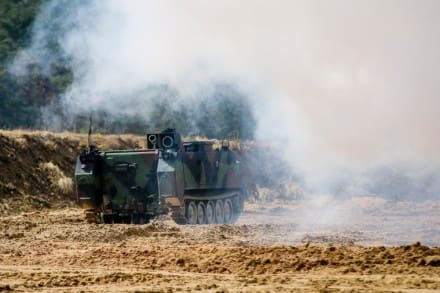
A M58 Wolf is remotely controlled to release a cloud of smoke during a multinational joint equipment U.S. military training exercise at Grafenwoehr Training Area, Germany, April 2, 2018 in preparation for a Robotic Complex Breach Concept demonstration.
The training event was conducted in preparation for a larger demonstration of unmanned capabilities, called the Robotic Complex Breach Concept, scheduled for later this week.
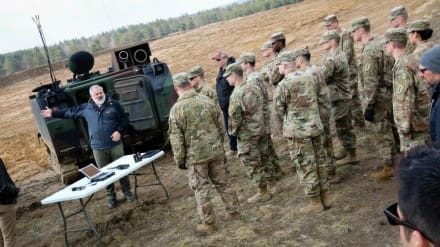
Ray Moldovan (left), a senior product management specialist with General Dynamics, explains to a group of U.S. Army Soldiers how to remotely control a M58 Wolf during a multinational joint equipment training exercise.
“Being able to take Soldiers out of harm’s way and accomplish the mission is very an attractive option to any commander,” said Curry. “It’s a capability that the enemy will not know how to counteract when we implement it. This type of technology enables us to stretch further while conserving resources,” said U.S. Army Lt. Col. Jesse Curry, commander of the 82nd Brigade Engineer Battalion, 2nd Armored Brigade Combat Team, 1st Infantry Division.
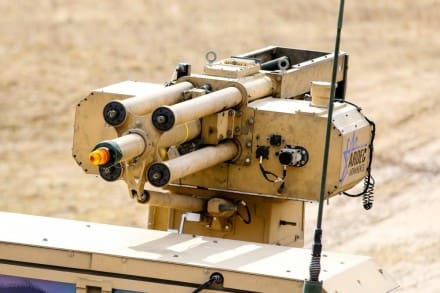
An automated direct and indirect mortar system is operated from a distance by U.S. Soldiers during a multinational joint equipment training exercise with the U.S. military.
The military-vehicle mounted Automated Direct and Indirect Mortar, the M58 Wolf Smoke Generator, and the ‘Terrier’ armored digger were some of the existing technologies used throughout the exercise. All were outfitted with new technology that allows them to be remotely controlled.
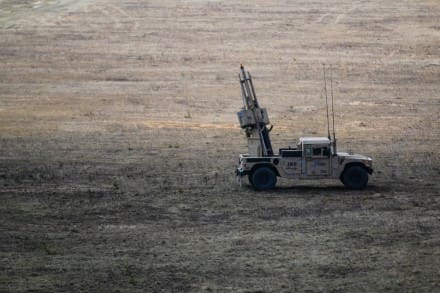
An automated direct and indirect mortar system is operated from a distance by U.S. Soldiers during a multinational joint equipment training exercise.
“This has been a great opportunity to show each other how to work on new systems, as well as each other’s systems,” said U.K. army Staff Sgt. Joe Ferries, a combat engineer with the U.K. 22nd Engineer Regiment, 8th Engineer Brigade. “All the lessons learned here are going to have massive benefits for our armies and the next mission.”
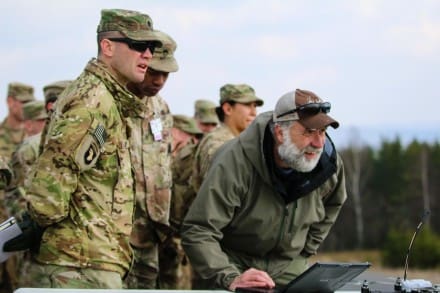
Mike Mackiewicz (right), demonstrates to U.S. Army Lt. Col. Jesse Curry (left), the commander of the 82nd Brigade Engineer Battalion, 2nd Armored Brigade Combat Team, 1st Infantry Division, the capabilities of an automated direct and indirect mortar system.
Ferries, the U.K. soldier who supervised a portion of the training, said he believes this kind of training is a natural part of improving any military.
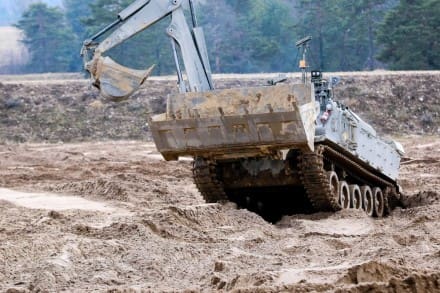
A “Terrier” armored digger from the United Kingdom’s 22nd Engineer Regiment, 8th Engineer Brigade is remotely controlled to secure an area.
“This training its quite relevant,” said Ferries. “We will always have to compare and improve our procedures and technologies.”
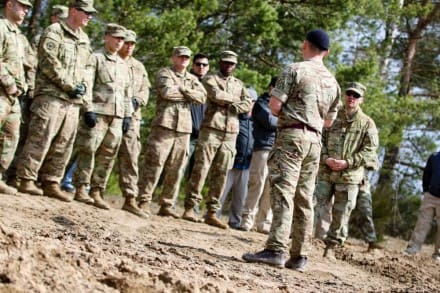
U.K. army Staff Sgt. Joe Ferries, a combat engineer with the 22nd Engineer Regiment, 8th Engineer Brigade, instructs a group of U.S. Soldiers, Marines, and Department of Defense civilians on how to remotely control a Terrier armored digger.
The U.S. Army’s 1st Battalion, 63rd Armor Regiment, the 82nd BEB, and the Maneuver Support Center of Excellence, and the U.S. Marine Corp’s Engineer School were among some of the units observing the training. Each unit’s service members got a chance to test the equipment and provide feedback to developers.
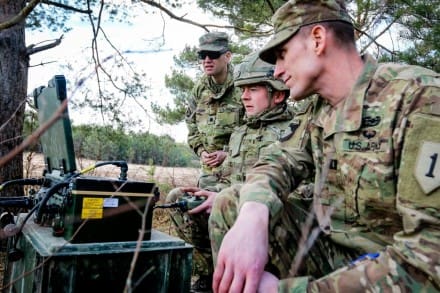
U.K. Lance Cpl. Tom Alexander (center), a combat engineer with the U.K. 22nd Engineer Regiment, 8th Engineer Brigade, shows U.S. Army Lt. Col. Jesse Curry (left) and Capt. Nick Hyde, both with the 82nd Brigade Engineer Battalion, 2nd Armored Brigade Combat Team, 1st Infantry Division, how to remotely operate a Terrier armored digger.
The Robotic Complex Breach Concept exercise will further test the capabilities of the new equipment, which is designed to enhance existing intelligence, suppression, obscuration, and reduction capabilities for breach operations.
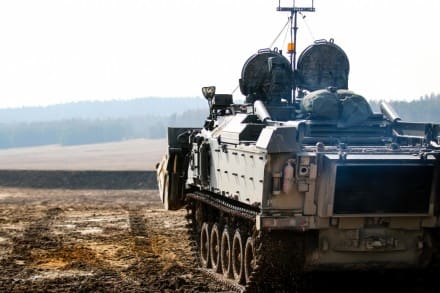
A “Terrier” armored digger from the United Kingdom’s 22nd Engineer Regiment, 8th Engineer Brigade, is remotely controlled during a multinational joint equipment training exercise with the U.S. military.
“This was testing of genuine and unique technology, partnered with cutting-edge development to address a complicated problem,” said Curry, who has served in the military for over 20 years. “Our potential enemy’s goal is to counteract what we have in our inventory, so we need to incorporate additional technology to enable our Soldiers to be successful in their jobs.”
Story and photos by SPC Hubert Delany
22nd Mobile Public Affairs Detachment