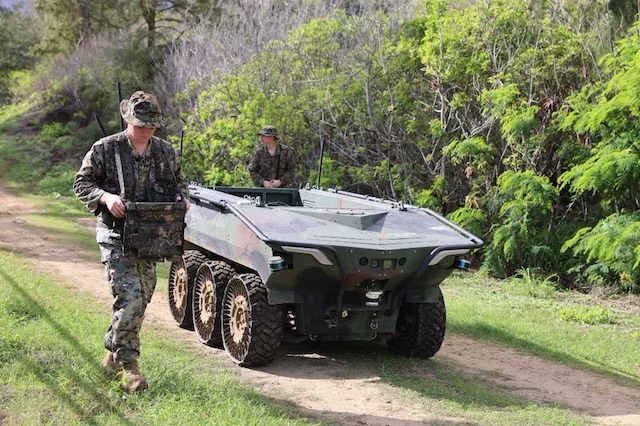
Marine Corps Training Area Bellows, Hawaii —
In a strategic move meant to advance Force Design’s shift to the INDOPACOM Area of Responsibility, the Marine Corps partnered with partners from the U.S. Army and the Ministry of National Defense of the Republic of Korea to test cutting-edge autonomous vehicle technology—taking a significant step towards modernizing its advanced logistics capabilities.
In mid-December, against the picturesque backdrop of Honolulu, Hawaii, Marines from the 3d Littoral Logistics Battalion, or LLB, engaged in a pivotal Foreign Comparative Test, or FCT, of a South Korean Unmanned Ground Vehicle, or UGV, prototype—marking a critical juncture in the Corps’ exploration of advanced unmanned technologies.
This two-week test, the culmination of a collaborative partnership between Marine Corps Systems Command, III MEF, the Army’s Ground Vehicle Systems Center and its South Korean allies, demonstrated the commitment to advancing military capabilities.
Key to advancing military capabilities, FTC programs allow the acquisition community to evaluate high-readiness technologies from foreign allies to quickly and economically meet defense needs. FCT stands out by offering substantial savings, bypassing research and development expenses, reducing procurement costs, and accelerating the deployment of critical equipment. This approach not only minimizes risk but also enhances the operational readiness and safety of U.S. forces.
The FCT of the South Korean UGV prototype in Honolulu is a significant milestone in the Marine Corps’ journey towards embracing unmanned technologies. This test, rooted in the principles of Force Design, and the ever-evolving realities of contested logistics, has the potential to shape the future of Marine Corps logistics operations.
“The use of autonomy directly supports Force Design, as the emphasis on smaller operational units means personnel have to do more,” David Keeler, MARCORSYSCOM’s advanced technology integrator for the Logistics Combat Element Systems portfolio and project lead for the effort. “UGVs can supplement tactical vehicle operations since they are highly transportable, can be moved to points of need quickly and don’t require licensed operators.”
As modern warfare continues to evolve, the need for efficient, autonomous logistics solutions becomes increasingly vital—especially as the warfighter is called upon to operate within contested environments. Here, the UGV’s potential to operate effectively in such scenarios stand to revolutionize how the Marine Corps approaches logistics, a critical component of warfare.
“If you look at the war between Russia and Ukraine, you see each side is going after each other’s logistics support. That’s contested logistics,” explained MARCORSYSCOM’s International Affairs Specialist Steve Duong. “What you don’t want is a big platform with a big signature transporting something like a tire or ammo back and forth because it can easily be identified by enemy sensors. A capability like this can help Marines with their logistics while operating in dangerous environments.”
Foreign Technology as a Force Multiplier
The test’s primary goal was to evaluate the UGV’s artificial intelligence and machine learning capabilities. The selection of the South Korean UGV prototype represents a leap in technological advancement, attributed to its maturity in utilizing artificial intelligence and machine learning to complete its mission.
“When we first started planning this effort, this was the most mature vehicle that uses artificial intelligence and machine learning to complete its mission,” noted Durgadath Nanan, III MEF science advisor, emphasizing the importance of these capabilities in current and future military operations. “This is an opportunity to get access to foreign expertise. Because, you know, we have great scientists, engineers and companies in the States, but that doesn’t mean we have the most advanced capabilities in all areas.”
This FCT is more than just an evaluation of a new vehicle; it’s a foray into a future where unmanned systems play a crucial role in military operations. The success of this test could lead to a transformative shift in how the Marine Corps conducts logistics, particularly in contested environments.
“Allied technology can provide tremendous benefits for not only the Marines and the DoD, but also to the vendors,” said Keeler. “Our vendors and allies get insight to our requirements and how their technology may be employed. Most importantly, it gives the vendors direct feedback and input from our warfighters so they can further refine and mature their technology.”
Joint Collaborative Effort
Keeler repeatedly emphasized the project’s foundation on innovative military technology and collaboration between Joint Forces and Allies. He acknowledged USMC’s International Programs Office for securing funding for the FCT from the Office of the Secretary of Defense and providing program support during the test cycle in Hawaii.
Nanan, a science advisor for the Office of Naval Research stationed at III MEF, played a crucial role as the liaison, ensuring ONR’s research align with Fleet requirements.
“We make sure that the R&D at ONR is working on requirements of the Fleet, not only short-term but longer-term,” Nanan said.
In Detroit, Michigan, DEVCOM’s Ground Vehicle Systems Center (GVSC) was instrumental in planning and executing the testing for the UGV project.
Jason Bagnall, GVSC electrical engineer and UGV FCT test lead, described GVSC’s involvement, saying, “GVSC’s robotics group has expertise in UGVs design, integration, and testing, leading the USMC to seek our independent evaluation of the South Korean UGV prototype.” He added, “GVSC developed the test plan, coordinated onsite activities, and will publish a report on the platform’s suitability.”
Ultimately, the project highlights the Corps’ commitment to international collaboration and innovation. As Keeler noted, “The FCT has been a great tool for LCES. It’s given us the opportunity to generate data to inform requirements, make procurement considerations, and build relations with allied governments and businesses.”
Feedback from the Fleet
The collaboration with 3d LLB Marines in testing and operating the UGV was a pivotal aspect of the project. Their direct, hands-on experience with the vehicle provided invaluable real-world data, shedding light on the vehicle’s performance, especially its sophisticated AI and machine learning capabilities. This practical insight from those with frontline experience was critical to understand the real-world applications of the technology.
Bagnall emphasized the importance of this partnership, further highlighting the importance of obtaining feedback from the fleet.
“Our in-house engineers and commercial/academic partners are some of the best in the business,” he said. “That said, most of our engineers have never served in uniform, have never experienced combat. When a mission is completely understood, and the doctrine well-established, it’s often possible for the user community to deliver really good requirement sets for tech developers to work from.”
Defining Future Requirements
Another critical aspect of this test is the defining of requirements for future unmanned ground vehicles. As Duong pointed out, “It is the major function of this test to help define requirements for unmanned ground vehicles, for which we currently don’t have a program of record.”
This endeavor aligns with the broader goals of the Corps to integrate more unmanned systems into their operations, as envisioned in Force Design.
“I have conducted a few different FCTs, each evaluating different technologies–from medical, to mine clearance, and now autonomy and UGVs,” said Keeler. “In each case we were evaluating an allied technology that either could close a capability gap, enhance existing capabilities, or provide a new capability.”
Keeler noted, if the FCT has good results, further evaluation in operational environments may be considered, followed by a decision to procure the technology.
The Broader Perspective and International Collaboration
The test also highlighted the significance of international collaboration, particularly with South Korea, a key ally in the Indo-Pacific region.
“This program is important as it falls under the security cooperation umbrella,” Duong said, acknowledging the 70th anniversary of the U.S.-ROK mutual defense treaty and its impact on such collaborations.
Nanan encapsulated the transformative potential of testing such advanced technologies, saying, “In testing this vehicle, we’re pushing the boundaries of what’s possible and confirming our commitment to be technologically advanced. This can change the way we operate and fight, adapting to the evolving nature of warfare as seen in current global conflicts.”
Ultimately, the successful testing of the UGV prototype marks a pivotal advancement in military logistics and unmanned technologies. This collaboration not only showcases the potential of international partnerships in enhancing military capabilities but also sets a new standard for the future of autonomous operations in contested environments.
By Ashley Calingo, MCSC Office of Public Affairs and Communication | Marine Corps Systems Command