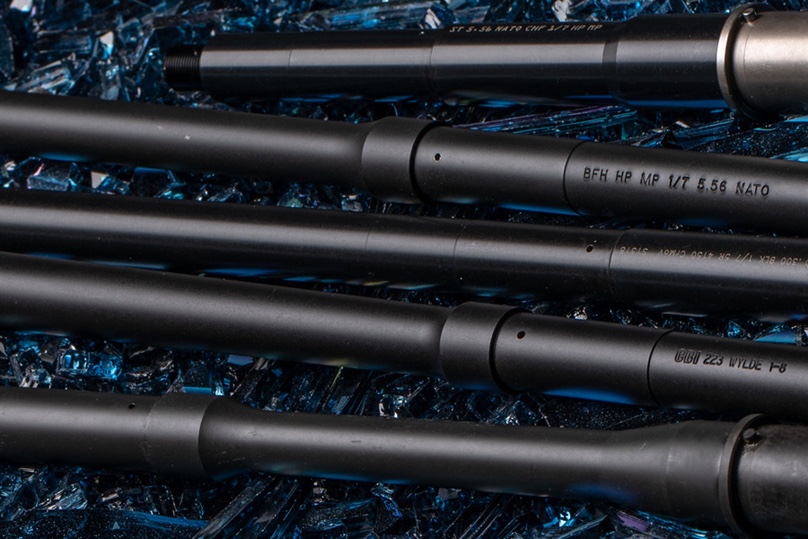
What’s the hype about .223 Wylde, and is it worth the money and time?
It’s not so much hype as reality. The .223 Wylde can successfully chamber and fire both the 5.56NATO round and the .223 Remington. The Multi-Cal on your lower receiver explained. Mystery Solved. Case closed – article over.
Unless you want the details…
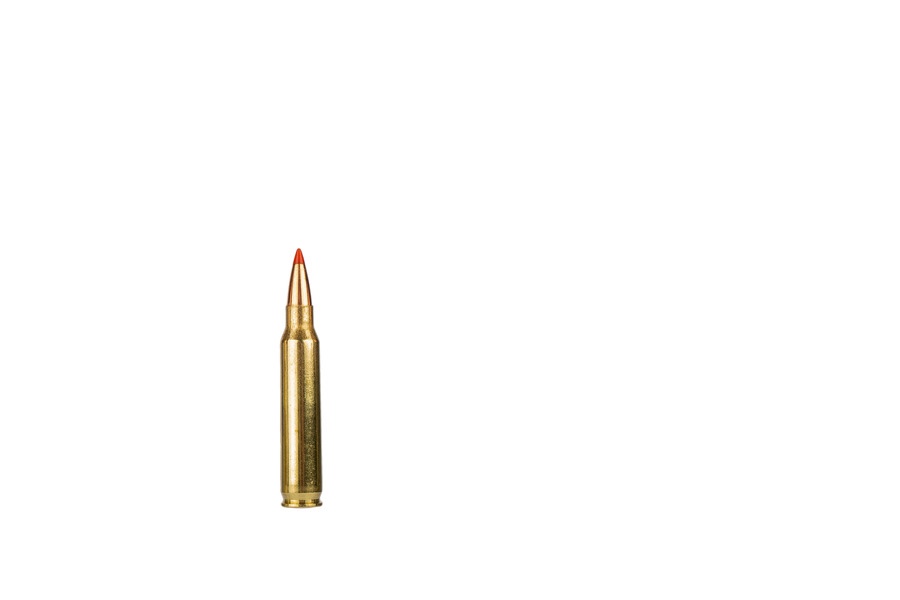
The 5.56×45 and the .223 Remington aren’t interchangeable. This is mostly because of pressure differences in the SAAMI specification. The load pressure for the 5.56×45 is 62,000 on the specification. The .223 Remington is loaded to a 55,000-psi pressure specification. The dimensions aren’t different, but the tolerances and the chambering dynamics are different.
All things equal, the .223 Remington is held to a tighter set of tolerances in expectation of being loaded into a firearm chambered to enhance accuracy and take advantage of that core tolerance control. The picture below shows 223 Wylde. They typically have a sharper taper from the case down to the bullet.
The 5.56 is held to a less rigorous tolerance specification and is meant to deliver a higher pressure load in its respective chamber.
So again, all things equal, the differences in potential are that the 5.56 is made for a higher pressure scenario and therefore requires a more supported chamber. The .223 Remington is built to a theoretical higher tolerance specification and can potentially be used to deliver better accuracy if given the right conditions.
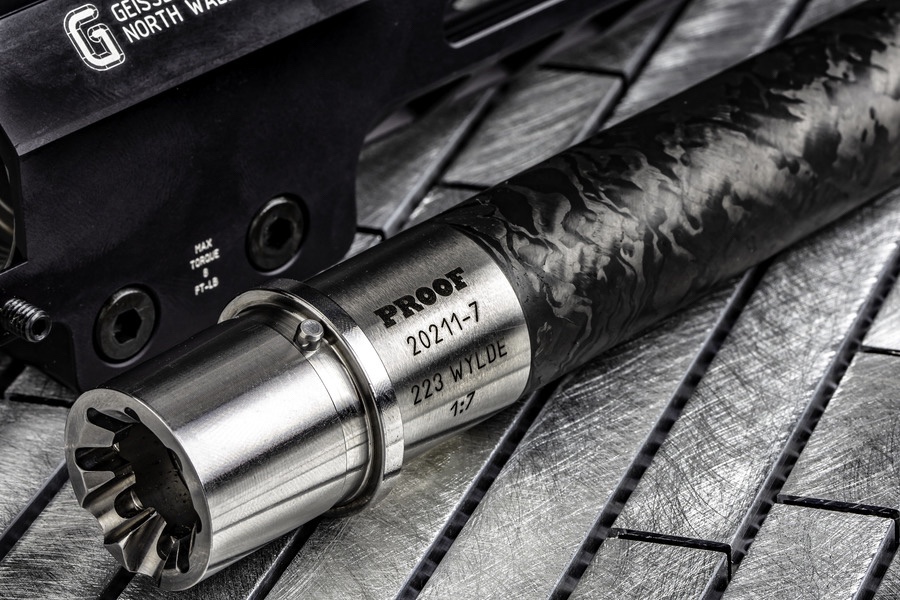
This is provable in the real world. You see it in ammunition prices (sometimes), and you see it on the target, more often. But the real benefit here is that safety and interchangeability that has been talked about for so long is part of the deliverables of the .223 Wylde.
What’s the point here? Sounds like something you could do safely with a 5.56×45 stamped barrel for years. Yes, in part, but not in totality. A 5.56 chambered barrel, while tough enough to handle anything it can chamber, doesn’t offer the same barrel-specific variables to enhance the accuracy that the .223 chambering will offer to the .223 Remington cartridge.
Similarly, the 5.56×45 cartridge should not be shot out of the .223 Remington chambering/barrel. This is already a higher pressure load. But the concern comes not from the higher pressure load, but the combination of a higher pressure load, and the higher pressure that will be stacked upon it from the fact that the 5.56×45 will be engaging the leade (the transitional part from the front of the chamber into the rifling of the barrel) incorrectly for the pressure specifications.
This means additional pressure will be present, even above and beyond the 62k psi that is part of the loadout.
In a .223 Remington, the leade is built to maximize the tolerance and quality control inherent in the .223 Remington cartridge from the factory. That engagement relies on a shorter space between the chamber and the rifling, where that transition will be too tight of a fit for a 5.56×45 relative to the tighter tolerances of a .223 Remington.
Does this mean your 5.56 will blow up a .223 Remington barrel or chamber? Not necessarily. It may never happen. But it’s a risk you shouldn’t be taking. The risk is real, and there have been accidents and failures, and it is a legitimate situation.
The backstory on the .223 Wylde
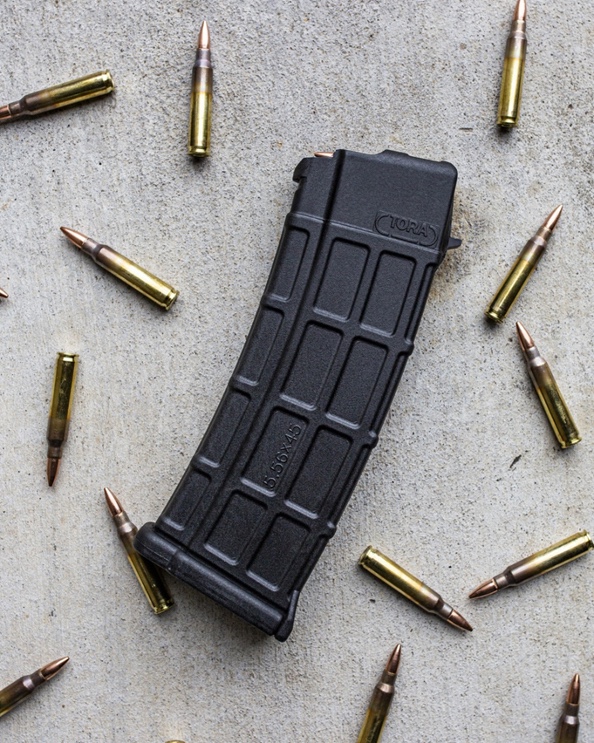
To get to the backstory of the .223 Wylde, you might be best served understanding the backstory of the .223 Remington and the 5.56 and how their paths crossed in 1972 when FN (the famous Belgian manufacturer) made a round-based off the .223 Remington for use by NATO that had preferable performance increases over the .223 Remington. This was due mostly to the higher pressure specification – 62,000 psi.
The benefit of increased range and effectiveness made the 5.56 the go-to for wartime and military usage.
The inherent accuracy though was lost from the .223 Remington, as it now had to be chambered in a chamber with different freebore and leade dimensions, which meant that the projectile engagement into the rifling of the bore was looser and not optimized for the .223 Remington.
Bill Wylde decided to modify the dimensions to suit the best attributes of each cartridge in hopes of finding a way to get the best of both worlds from either cartridge in a single barrel suited to handling the intricacies of both cartridges independently or in use together.
The leade and outer dimensions of the 5.56 barrel were used to compensate for pressure and allow for the proper chambering, while the freebore of the original specification for the .223 Remington was used to ensure safe engagement but still support the tendencies of the .223.
The result was improved effectiveness on the accuracy front for the .223 Remington, in a barrel specification that could safely chamber and shoot both cartridges with reliability and the performance that was only slightly lacking over the previous optimized standalone accuracy of the .223.
Basic performance ranges and off the shelf type performance parameters
Each cartridge is going to get similar performance metrics out of the Wylde. It isn’t overly compensating for anything. Where you will see some important performance increases is with the .223 being slightly more accurate than it was having been used out of a true 5.56×45 specification chambering.
It also allows for the higher grain weight and slightly elongated 80-grain projectiles that are popular in National match type events to be shot particularly well from the barrel and therefore gives niche shooters a way to optimize further for longer range more effective projectiles on hand loads or specialty factory loads for longer range targets.
What’s the incremental cost increase and does it pencil out logistically?

It depends on what you are trying to accomplish with your rifle. It’s simultaneously a good way to be sure you get good performance from both cartridges out of a single barrel and to utilize an optimized build to prioritize larger grain weight bullets that are particularly good on long-range targets in competitions.
That is where the market has determined the Wylde should be at this point, and there are enough shooters in that niche or with the desire to play around with the stability and accuracy of the larger grain weight projectiles that the Wylde chambering has become an interesting option to a growing market population.
Only you can decide if the cost of a barrel will ruin the economies of your engagement in the varied aspects of the AR market.
What can you do with a .223 Wylde that you cannot do with other chamberings?
Shoot safely, and extract maximum theoretical precision from any given (safely) chamber-able cartridge from either the 5.56×45 or the .223 Remington. You can also hone down on the optimization for larger grain weight bullets suitable for competition that have a longer overall length.
Some basic optimization considerations for the .223 Wylde
The competition group has become so hyper-focused on tangential optimization strategies that a whole subculture of customization now exists that can cut a freebore by a few thousandths of an inch for a specific chambering to match a specific projectile, and specific Overall Cartridge length projectile included.
The importance to some shooters is so high on these dimensions that they are custom handloading rounds to that given specification in an attempt to wring out the most accuracy from the specific pairing.
While it may seem a bit esoteric, the tangible benefits are evident through data collected by volume shooters of precision builds in competitions like the National Match formats.
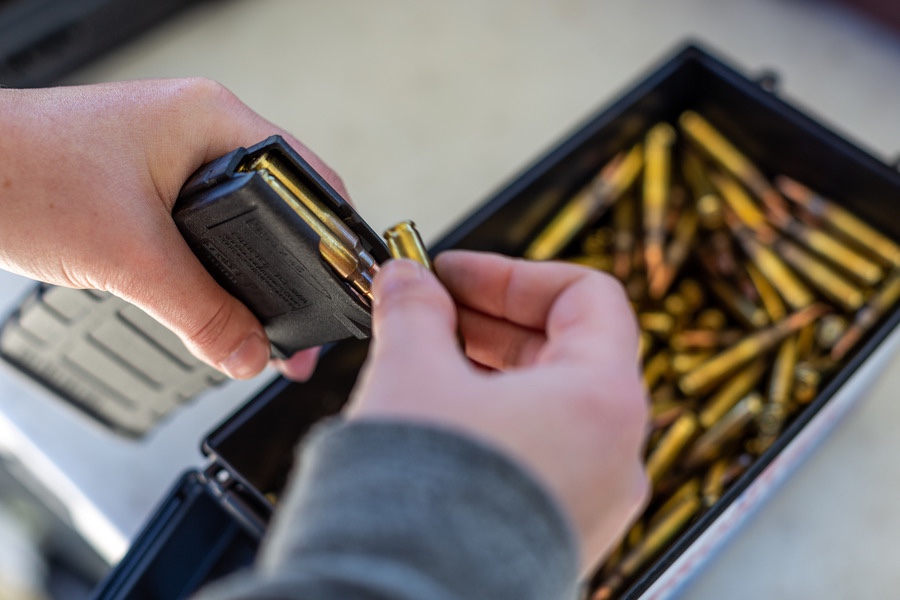
In a broader sense, the mainstream adoption of ever more optimized and nuanced parts and components in the AR space allows the consumer to further tailor their modular build to their unique needs, even if that incremental improvement may not be registering in the overall data.
This is not a criticism of the Wylde concept; the people who strive for absolute precision in their components and the variables they build for their style of shooting; or the market for AR component parts.
Rather, this is an exploration of what is possible when a modular platform like the AR can begin to make improvements on an already ridiculously refined set of components to further defy the pundits of the AR market and sell more nuanced and sophisticated elements to a group that likes to test everything.
The Wylde equals the playing field for the .223 Remington, which was made for higher tolerance guns, and the 5.56×45 which was made for cyclic reliability. It melds the best of both worlds to create a space where innovation might be derived.
Getting a bit more into the weeds about how the Wylde Chamber can be optimized – you will typically find the chamber matched to a rifling twist rate of 1 in 8 inches, which is traditionally mated to projectiles in the 75 and 77-grain arena.
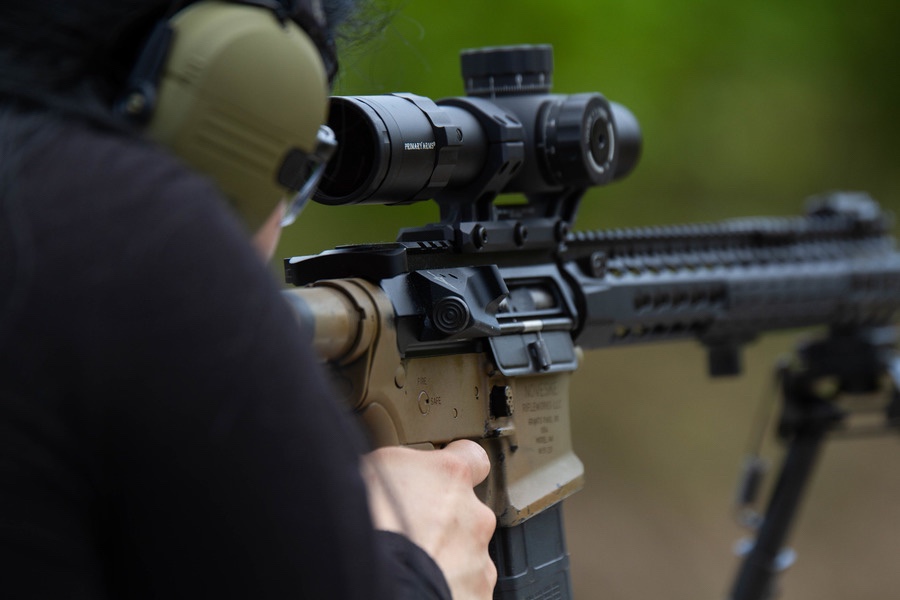
You’ll also have access to the 80-grain specialty match bullet – the storied Boat Tail hollow point by Sierra Match King that has quite the reputation, which is also being optimized over a decent range of velocities. The twist rate is good for stabilizing the longer bullets and the specific angles of these types of projectiles.
The 1:8 twist is particularly forgiving and doesn’t over or under spin the projectiles in this range, giving the handloader the ability to find a standard deviation range that works best for their specific goals on the range and specific distances, taking the barrel out of the equation and giving the corresponding control over flight to the handloading precision of the ammunition maker.
Conclusion
Such is the state of the competitive market in the AR space – and that is said without a hint of sarcasm or frivolity. Individual shooter control where there was never control given before, is a benefit to those who will optimize it. That may be the best storyline about the Wylde that we can think of.
Primary Focus is a weekly feature from Primary Arms that covers various firearms related subjects.