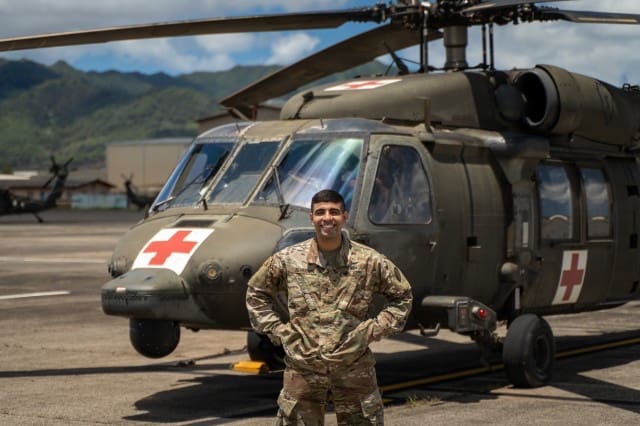
WHEELER ARMY AIRFIELD, Hawaii — Mahdi Al-Husseini had his whole career figured out as he enrolled in Georgia Institute of Technology back in 2013. He knew he would graduate with a joint degree in biomedical engineering and public policy before attending graduate school for computer science.
From there, he planned to pursue a job in the defense and space industry.
The idea of joining the Army never once crossed his mind, he said. He knew nothing of his school’s Reserve Officer Training Corps, or ROTC, and the vast opportunities in the Army.
Now a first lieutenant, Al-Husseini serves as an active-duty aeromedical evacuations officer with 3rd Battalion, 25th Aviation Regiment at Wheeler Army Airfield, Hawaii.
He is also an engineer currently developing an aerial hoist stabilization system that could help save lives during an in-air medical extraction.
“There is something unique about the medevac mission,” he said. “We ensure that America’s sons and daughters — individuals that have experienced great tragedy — have an opportunity to return home.”
Best-laid plans
While Al-Husseini’s passion for engineering never wavered during college, he did find a deeper calling to support something greater than himself.
The Army quickly soared to the top of his list, as he joined ROTC during his junior year. He was determined to give back to the people and institutions that helped him succeed.
“After I joined, I was deciding between a few different Army branches: medical services, engineering, or cyber,” Al-Husseini said. “That same year, I interned at the U.S. Army Aeromedical Research Lab.”
The USAARL looks to deliver scientific solutions to help save lives, according to lab officials. Research efforts target biomedical, physiological, and psychological issues, as the Army aims to increase the performance of aviation, airborne, and ground personnel.
As an intern, Al-Husseini assisted the lab’s experimental testing efforts tied to various aviation helmets. He eventually crossed paths with two medevac pilots working on a separate project. The three became friends as they started to exchange ideas.
“This was the first time I talked in depth about the medical evacuation mission,” Al-Husseini said. “We are responsible for bringing home America’s wounded warriors. In my opinion, this is truly one of theArmy’s no-fail mission sets.”
Influenced by his peers’ passion and drive, Al-Husseini’s outlook on engineering and his future career decisions started to shift.
“My experience [with USAARL] cemented my interest in the aeromedical mission. I decided to request medical services as my first choice of branch,” he said.
“I [now] look at engineering and computer science as tools in my toolbox,” he added. “I love engineering and computer science … but as an engineer, you have to decide what to do with those tools.”
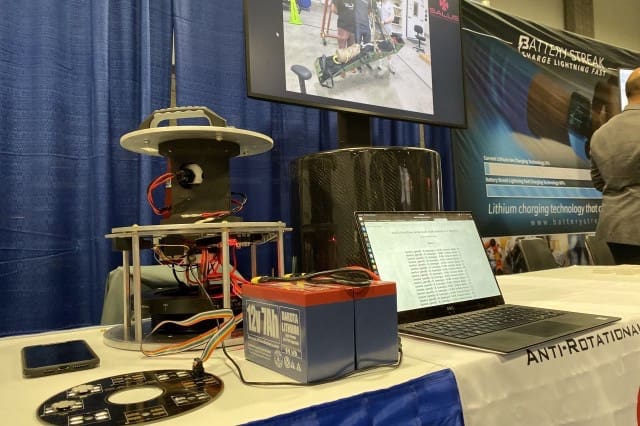
Training, engineering, competing
Shortly after college, Al-Husseini found himself at Fort Rucker, Alabama, for flight training. It was around the same time that he started building his own company, a combined team of Army aviators and engineers, to develop their Stabilizing Aerial Loads Utility System.
“When we perform a medical evacuation on a real mission, usually it is the worst day of a patient’s life,” he said. “I wanted to use my skills and tool in a way that supports these Soldiers.”
During an in-air medevac mission, pilots are trained to control the aircraft as the hoist-line sways from the downward force of air created by the vehicle’s rotor system. Commonly known as downwash, this aerodynamic force can cause the hoist line to spin or oscillate, putting a patient or operator at risk.
“There have been fatalities connected to the spin, sway, or oscillation of the hoist line,” Al-Husseini said. “There have been a lot of folks that are negatively affected, either through asphyxiation, fatigue, or nausea. These real problems are impacting our patients, which are already in a compromised state.”
The new hoist-line system is designed to connect between a patient’s litter and the line’s base. The device’s internal control system will help stabilize the patient through a series of automatic spinning reaction wheels to counter the hoisted load movement.
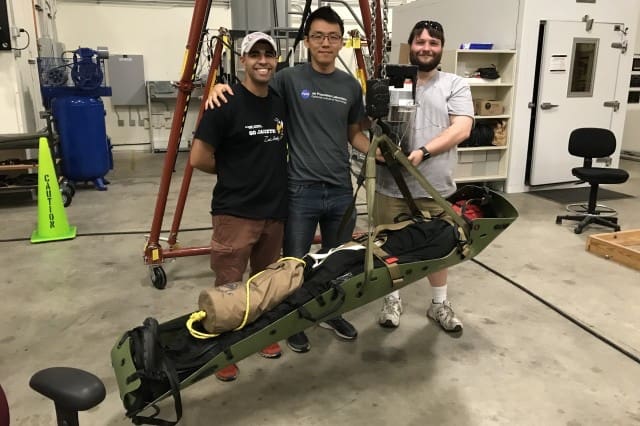
As Al-Husseini continued through flight training, he split himself between two worlds. He spent most of his time learning to be an aeromedical evacuation officer, and then his free time on his invention.
He credits much of his success to the overwhelming support he received from leadership and colleagues during training and his career, including Capt. Kimberly Smith.
“It is amazing to see everything that he’s done and accomplished, all while learning how to fly,” said Smith, commander of Company D, 1st Bn., 145th Avn. Rgt. at the Army Aviation Center of Excellence.
Al-Husseini remained committed to his team as they entered their new aerial load system into several competitions, including the Army’s xTechSearch.
“The xTechSearch program is incredibly well run,” he said. “It is so important to the many small businesses that are working to develop technology” that might aid in the Army’s future.
The Army’s acquisition process can be confusing and overwhelming for a smaller business, he added. Through the competition, small business owners develop connections and can earn possible funding for a specific program.
“It is an exciting time to be in the Army right now and be an engineer,” Al-Husseini said. “The Army is working to improve on a technical level, and the xTechSearch program is a model blueprint” for the way ahead.
To attend these competitions, Al-Husseini had to request a delay in training, Smith said. Pausing a Soldier’s education could negatively impact their career, and is typically granted on a case-by-case basis.
“When you are on the flight line, it can definitely become very challenging. Your purpose is to learn how to fly,” Smith said. “I always preach to the students: you have to find balance.
“I am impressed that [Al-Husseini] managed all of flight school and graduated, all while designing a device that could be beneficial for the Army,” she added.
Currently, the device from Al-Husseini’s team is being evaluated by USAARL. If selected, it could become a vital tool in support of the medevac mission, he said.
Seeing the device on an Army aircraft, “would be a dream come true,” he added. “Not for myself and the success of my team, and not for any financial gain. Just knowing that each Soldier will be better off because of what we developed … is more than I could possibly ask for.”
Alternatively, if his device does not meet the Army’s final selection process, Al-Husseini would applaud the decision.
“I do not want my device to be selected if there is a better device that exists,” he added. “I want whatever is best for our Soldiers in the field. That is what it means to be an engineer. You have to continue to scrap your designs or refine to pivot and to create new ideas.”
Overall, Al-Husseini said, the Army is a diverse force full of incredibly inventive and resourceful people.
“Identify a problem and find a way to solve it,” he added. “You will be amazed at how supportive the Army can be. I think this is one of the things that makes our Army the greatest in the world.
“I want to encourage Soldiers to think outside the box and continue to push their limits to find ways to improve their organization. Because at the end of the day — no one knows their mission set better than they do.”
By Devon Suits, Army News Service