FirstSpear’s cummerbund offerings provide enhanced modularity, speed, and protection to support a variety of mission profiles. Each cummerbund is purpose-built to enhance FirstSpear’s plate carriers, providing mission-driven adaptability, protection, and rapid gear access.
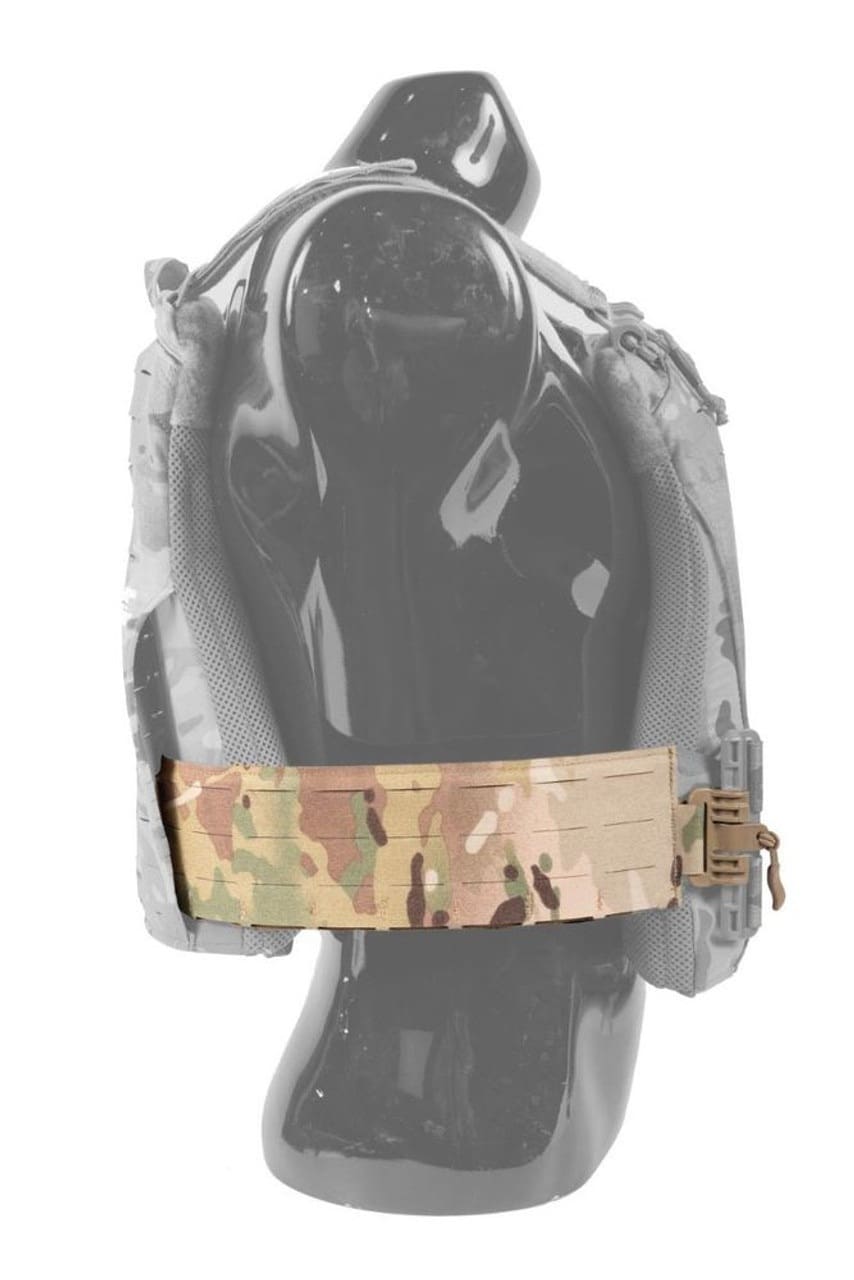
The RIGID CUMMERBUND is designed for rapid donning and doffing using 2” Tubes, ensuring compatibility with all Tube sizes. Built to integrate seamlessly with the Instant Access Back Panel, it enhances load carriage efficiency with an exterior 6/12 attachment field for modular pocket configuration. The interior loop field allows for the attachment of FirstSpear’s Ragnar pockets, providing additional storage options while maintaining a low profile.
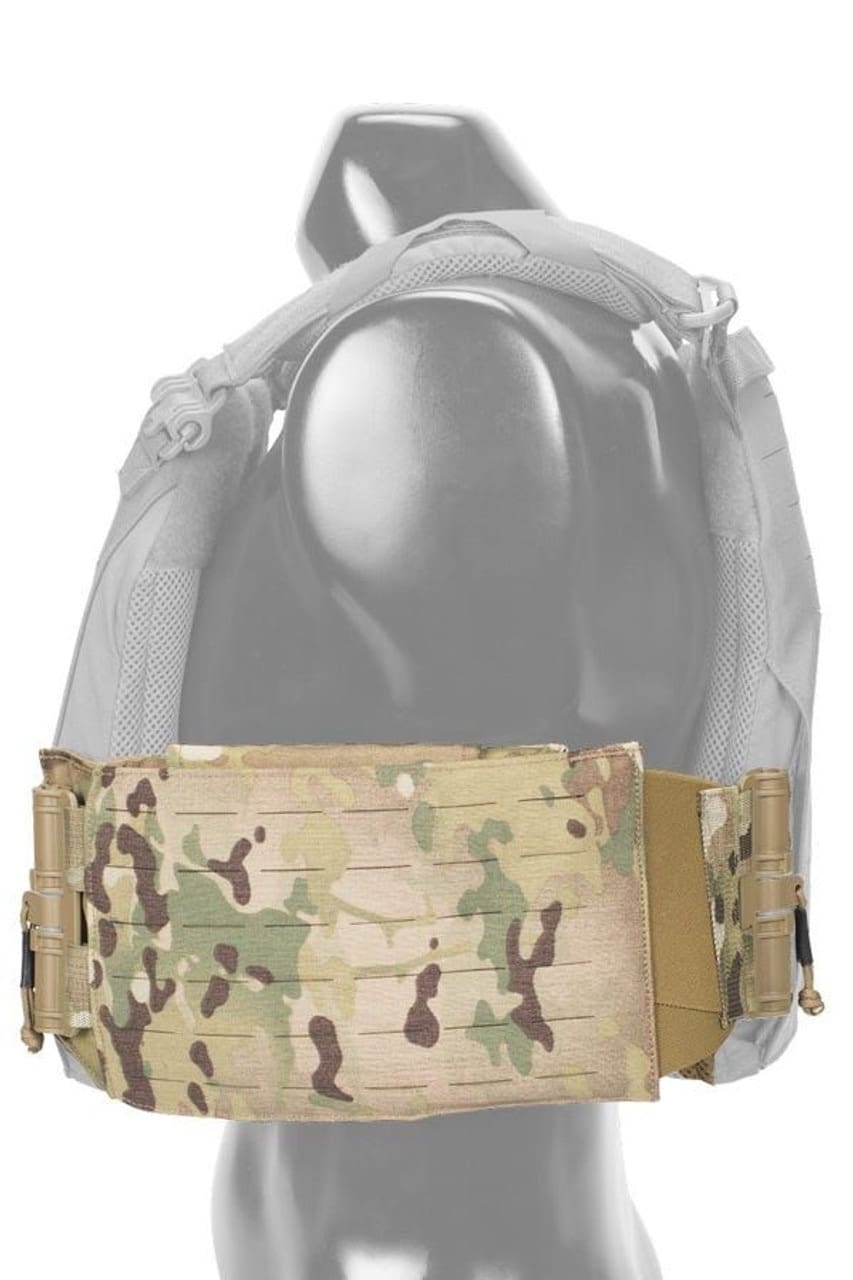
The ADAPTIVE CUMMERBUND is built for maximum flexibility, allowing users to quickly swap between land and maritime configurations using Tubes technology. With Tubes on the front, this cummerbund requires the TUBES™ RETRO-FIT CUMMERBUND, ATTACHMENT PANEL, enabling users to set their fit once without repeated adjustments. Engineered to support soft armor inserts, it provides mission-adaptive protection without sacrificing speed or efficiency and eliminates the hassle of hook and loop, allowing for near-instant transitions between operational setups.
The OVERLAP CUMMERBUND enhances protection by providing additional soft armor coverage where the Tubes connect, ensuring greater security without compromising mobility. Designed for seamless integration with various FirstSpear carriers it optimizes load carriage efficiency. The interior allows users to keep magazines and gear close to the body, creating a streamlined profile ideal for confined spaces and dynamic operations. This cummerbund supports modular attachments through FirstSpear’s 6/12 technology, further enhancing customization, and was designed to benefit users needing expanded magazine capacity beyond front-loading setups while maintaining full vest functionality.
The RETRO-FIT CUMMERBUND brings the advantages of 6/12 and Tubes® technology to carriers that use traditional hook and loop flap systems. Designed for seamless integration, it allows users to upgrade their load carriage platform without needing an entirely new vest. This cummerbund supports soft armor inserts and 6″x6″ hard plates, enhancing protection while maintaining a lightweight and modular design. Included in the kit is the OVERLAP CUMMERBUND and all necessary attachment components, making installation straightforward. With its innovative design, this cummerbund provides a secure, adaptable, and modernized fit for users seeking enhanced functionality in their existing carrier systems.
FirstSpear is the premier source for cutting edge-tactical gear for military, law enforcement and those who train.
For more information visit First-Spear.com.